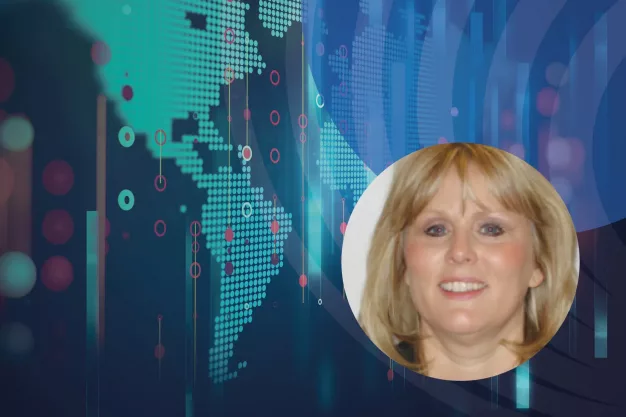
Meet the Team: Susan Bellomy, Channel Director, Ripley Tools
1st July, 2022
Having spent more than 20 years in the business of selling tools – including in sales and distribution positions – self-confessed “people-person” Susan brings
At Ripley Tools, we’re incredibly proud of our expert engineers at Ripley Labs, but they’re often so busy developing new products for our customers that they rarely have time to share what they’ve been working on.
We know that our customers love to hear about what’s happening behind the scenes – so we sat down with Brian Bourgoin, our Director of Engineering, to ask him all about Ripley Labs.
“There’s always lots going on at Ripley Labs, which makes it a really busy and exciting place to work. We often invite our OEM customers to the labs to talk to us about the tools they need and the new cables they’re developing, and these discussions often give our engineers new design ideas, as well as ideas for how we can take our existing tools in new directions.
When we have an idea for a new or existing product, we’ll use the factory support manufacturing team to generate rapid prototypes in order to bring the concept to life for our customers and our team. We’re also constantly testing our tools within the lab, because extensive testing is a crucial part of our product development. We’re proud of our reputation for providing quality tools, so before we launch our tools they go through a rigorous program of strength, load & performance testing.
We also carry out a lot of training sessions at Ripley Labs, and our training area is equipped with cameras so that we can carry out remote training, too.”
“Ripley Tools has always been an innovative company. Over the years, we’ve secured almost 90 patents on our fiber, cable tv and power utilities tools, so we have a long history of developing new tools that are truly original in their design.
With cables evolving rapidly and engineers facing new challenges every day, we established Ripley Labs to ensure that our engineering team had everything they needed to continue producing original, high quality tools to meet our customer needs. We also wanted to create a state-of-the-art space that would enable our engineers and our customers to come together creatively. Four of our patents have been secured in the past five years alone, so we’re clearly doing something right!”
“When we’re developing new tools, precision is really important. We want to make sure that the job is repeatable and reliable so whatever an engineer is doing – prepping a fiber optic cable or a power utility cable running thousands of volts – they’re not going to damage the joints. With our highly precise tools, they can create repeatable joints and get the job done quickly and safely. That’s always been what has set Ripley Tools apart, and that’s still a key priority for us today.
Over the past few years we’ve also been focusing on modernizing our designs. Some of our older generation tools utilize castings, which gives them the robustness that engineers need. But we’ve been introducing more plastic tools when appropriate because it allows us to be flexible in our designs and to boost the ergonomics of our tools. Engineers want light tools that are comfortable to use, so that’s always a key consideration for our team.
We’re also always thinking about how we can design our tools to be as cost-effective as possible without sacrificing performance. We know that cost is another important factor for engineers, because while they need tools that are safe, comfortable and precise, many are also keen to keep their costs low. When they choose Ripley Tools, they know that they’re investing in a tool that gives them real value for money.”
“It’s all in the testing. When the patent was due to expire on our ACS tool, for example, we saw a great opportunity to redesign it with a whole host of new features. The original ACS was aluminium, and we decided to make the ACS+ in reinforced plastic, because you can incorporate more features into plastic than you can with cast aluminium.
We were able to come up with something that was just as strong as the aluminium tool by undertaking a finite element analysis in the design stage before we even commit to a design, and then rigorously testing at every stage after that. So although we consider plastic tools for a range of reasons, we’re ensuring that our tools are just as high-quality and robust as they have always been through our testing processes, and of course we always utilize metal components when necessary.
We work incredibly closely with the quality department to validate and inspect the parts used in all of our tools, which ensures that they’re holding their tolerances once they go into production. We’re also ISO certified, which gives us a strong framework when it comes to our quality assurance processes.
We also use customer feedback to ensure quality through our demo on demand program, in which engineers can try out a range of our tools for 30 days for free. At the end of their demo period, we talk to each customer to find out what they think about the tools they tried. By listening to their feedback, we can ensure that our tools are always meeting engineers’ needs – and if we identify any areas for improvement, we’re always open to bringing existing tools back into the lab to test new ideas.”
“Over the past few decades, engineers have come to expect the tools they use to be comfortable, and they have certain expectations for how a tool should feel in their hands. Efficiency has also become increasingly important, so engineers are looking for tools that can help them to get the job done more quickly – every tool in their kit must be easy to use, with repeatability and high precision. Of course, they also need their tools to be light, balanced, and ergonomic.
In recent years, we’ve been getting more requests for drill operated tools. We’ve always had drill adapted tools, but now engineers want tools with integrated drills, such as the US16. Being a linesman is a physical job, particularly for those in the utility sector, so it’s not surprising that engineers are turning to automation to take the strain out of stripping cable.”
“We usually bring utility and fiber companies into the lab to talk to them about the gaps they’ve identified in the market and our ideas for new tools. Often, OEMs come to us with a cable that’s mid-way through the development process, as they’ve realised that there isn’t a tool on the market that can give engineers access to the cable. Obviously it’s vital that this tool is created before the cable is launched, so we’ll work with them to develop a tool that fits their unique cable.
Sometimes this involves creating an entirely new tool, but often it’s a case of tweaking our existing tools to enable engineers to use them on new applications. A big part of our work at Ripley Labs is application support – our customer service and technical support teams are constantly receiving requests for tools to support new cables, and we’re always up for the challenge.
If we need to create a new tool from scratch, it will go through our extensive new product development process. First, we’ll brainstorm concepts, and consider whether there would be an appetite for the tool in the market. Then we’ll take the tool through concept development, prototyping it and putting it into testing. The testing stage is often iterative, with designs sometimes going through multiple revisions as we develop them. Once our vision for the design stabilises, we’ll create a prototype, and use that prototype to carry out a final design review. If the tool passes that review, it’s ready to go into production! The entire new product development process takes place within Ripley Labs at our Connecticut headquarters – so you can see why it’s a busy place to work.”
“We invested in a state of the art, commercial quality 3D printer that has production-quality tolerances. This means we can get production-quality parts out of it, which really accelerates the time to prototype. With 3D printing capabilities on-site, we can take a concept in 3D CAD, press a button and have a physical part within hours.
It’s really helped us to speed up the design process, because it enables us to get a feel for a tool design and quickly identify areas for improvement. Before we had the 3D printer, we’d have had to wait for the machine shop to create the tool before we could get that insight, so it’s really enabled us to move through the design process far more efficiently.
It also helps us to be more creative. When we had to send a design to the machine shop, we tended to be more conservative in our designs, but as it’s so easy for us to produce a tool using the 3D printer, we can test out some more original ideas.
Sometimes customers ask us to provide them with 3D printed tools if they just want a small run or to use a tool for a specific project, for example. These tools don’t have the full durability that our main tool lines have, but if they’re used on a project where there’s not going to be a high load, they are just as effective as a production plastic or metal tool from our machine shop. Some jobs simply require tools with high accuracy and precision, which means that tools that are made of 3D printed material are perfectly functional for the job.”
“In the weeks and months after we release a new tool, we’ll focus on training our customers to get the most out of the tool. We produce training videos to help customers to get to grips with new tools, providing them with hands-on demonstrations so that they can see how the tool’s features come into play. We also train our distributors and representatives on the tool, so that everyone understands how the product works and what it’s used for, so they can advise customers.
After that, we simply listen to our customers to ensure that the tools we create continue to meet their needs for the long-term. We’re all about continuous improvement – and when a tool is copied by others, we see it as a challenge to take that tool to the next level. So we’re constantly considering new ideas for evolving our existing tools.
Of course, sometimes cables evolve to the point where we can no longer simply adapt an existing tool design, and instead we need to create an entirely new tool. That’s why we work closely with OEMs to ensure that we’re at the cutting edge when new cables are launched, so we can quickly provide tweaked tools or new tools that suit the latest cables.”
“I can’t choose just one, because we’ve had a lot of exciting new tool launches within the team recently. So my top three would be:
The MB02 – which is exciting because we have a patent pending, and we truly believe that the mousetrap is better than any other in the market today. This year, we’ll be working on the MB02 further to make it more versatile and applicable to a greater number of applications.
The US16 – which was fun because it was a complicated product and we did a lot of design work on it. When Andy – the lineman that originally came up with the idea – brought it to us, it was a great idea but needed some work before it could become a mass market product – we totally redesigned the blade, for example. It’s just launched, and we were so pleased to see such a great reaction from our customers.
The ACS+ – this was a great project because it was a chance for us to take an old design (the original ACS was developed over 15 years ago) and refresh it. The original lead engineer of the ACS is still working for Ripley, and he was the lead designer on the new project, so he was really excited to evolve the product all these years later.”
“We’re seeing a real increase in the bandwidth and density of telecoms cables. This means that over the coming years, precision will become even more important than it is now, as the air gap between fibers and components becomes smaller.
Tools will need to perform more accurately because cables are going to be much more densely packed – so testing and precision will continue to be a key focus for our team.”
Interested in working with the expert engineers at Ripley Labs? Whether you’ve got an idea for a totally new tool, or you need a tool to fit a new cable, they’re always up for a challenge – click here to schedule virtual or in-person lab time.